电子器件的市场趋势
当前,电器和移动AV设备市场上,智能手机和平板PC成长迅猛。智能手机的全球销量从2012年的6.5亿部增加到2013年的7.9亿部。预计2015年将达到10亿部。类似地,PC的全球销量从2011年的1.2亿台增加到2013年的1.6亿台。预计2017年将达到4.2亿台。这些移动设备要求一年比一年更高的性能、更多的功能和更低的价格。所以,用在CPU、GPU、DSP、AP和RF中的半导体产品规模更大,速度更高、更加密集。为此晶圆工艺技术正通过加大晶圆尺寸(即从150mm扩大到300mm或400mm)减少成本,并通过更细的工艺图形(即从90nm到65nm、45nm、40nm、32nm和28nm)改善至更高的集成度、功能性和速度。故与此同时要求更高的电路密度、更高的性能和更低的价格。
对于集成度较大和速度较高的LSI的成熟技术,有必要开发采用低k材料的隔离技术。但为了满足这些高性能,由于用多孔和多层结构,隔离变得越来越薄。结果,LSI就变得易脆。另一方面,为了满足高速要求,LSI的电流不断增加。除了芯片尺寸不断缩小外,热密度和功耗也不断增加。所以,对于未来的半导体封装,要求解决这些问题,即层间介质的易脆性、高热、高速和低价格。半导体工艺未来的设计规则将进入20nm一代或其下,这将更加脆弱得多。
20nm一代要求的封装技术
下一代20nm要求的规范为:
低应力,为了易脆低k层
高热辐射≥5W,为了高性能LSI
高速度≥10GHz,为了高功能性
半导体封装趋势
为了适应包括移动设备在内的电器设备的功能提高和成本下降,晶圆设计规则朝着大尺寸和细设计规则发展。为此以及为了降低成本,半导体封装技术正迅速从最标准键合技术的金线键合转移到铜线键合,以减少金的使用量。此外,倒装芯片键合技术的使用大大地满足了LSI的更高集成度和性能。2010年,全球半导体封装技术中,倒装芯片键合的份额为15%,引线键合的份额为85%。而到2015年,预计倒装芯片键合的份额将达25%,引线键合的份额将为75%。特别是对于要求高热辐射和高信号速度的高集成度高性能LSI,正积极地采用倒装芯片键合技术。
常规倒装芯片技术的问题
对低k的适应性
通常使用的倒装芯片技术:
● 焊接连接,主要结构是C4(可控塌陷芯片连接)
● 对于Au凸点和ACF一类的压力键合连接
● 对Au-Au一类连接的超声键合连接
压力和超声键合有高压力和机械振动加于LSI,所以这些方法不能用于低k LSI。因此,在上述方法中,C4是可以采用的,因为比较这三种方法,键合时C4对芯片的损伤最小。
C4技术是40年前为通用计算机发明的,一直使用至今。随着低k晶圆的不断增加,通过替代UBM(凸点下金属)结构、材料和及其改进,将C4用于低k。
最近开发的Cu柱凸点(类似C4的发展)是适应直列或错开焊盘版图,不是对低k 晶圆的。有报道说,Cu柱结构封装可能破坏低k层,这是由于Cu的弹性模量高(130GPa)。热膨胀系数(CTE)不匹配是其加速因素。
此外,C4技术起初是通过焊剂和焊剂的高弹性模量(50GPa)采用熔融金属结,所以,在对母板键合和安装时,由于热膨胀的差异而加到LSI 大量应力。故C4技术不能用于未来更为脆弱的LSI。
热辐射
目前,用于倒装芯片封装的主要是有机基板。有机基板的热导率很小,为0.5 W/mk,很难应用于高功耗的LSI。如果为了改善热辐射而附加散热或冷却系统,封装的成本、面积和高度都将增加。
实际上,由于热辐射低,有一些LSI限制了其潜能以便不产生大量的热。此外,由于热辐射不良,结温度升高,使得漏电流增加,这进一步使功耗增加,功耗的增加又使其温度上升。这是一个危险的恶性循环。所以,改善热辐射是一个重要问题。
信号的高速度
有机基板核心层介质损耗高(0.02),核心层通孔(T/H)的阻抗高,结果,在高频范围的插入损耗高。但是,使用传统有机基板相同材料的无芯基板不是根本的对策。此外,组合层材料可以各式各样,所以,用户选择最佳材料就更为困难,整个设计要求考虑高速性能。
而由于基板薄,需要改变一系列的设备。这就成了生产的障碍。由于这一问题,转移到无芯基板是有高风险的,仅能适应部分产品。
传统的技术难以满足未来20nm一代。所以迫切要求以新的核心技术开发全新的半导体封装。
MonsterPAC-typeC及工艺要点
为了满足传统封装技术难以适应的20nm工艺,我们开发了MonsterPAC-typeC。这是与传统封装工艺与结构完全不同的封装。
封装结构
我们的封装结构,基板是陶瓷的,半导体芯片用凸点倒装,芯片与基板之间填充NCP(不导电浆料)。没有用环氧树脂一类的模塑。所以芯片背面是暴露的。再流焊一类的高温翘曲是小的,低于30-50μm,所以这种封装是没有焊球的LGA(触点阵列封装),不是BGA(球栅阵列封装)。含银导电浆料用作凸点,这些凸点印刷在基板上,故在焊盘上不再制作板块。不需要晶圆凸点工艺,仅在芯片的Al焊盘上非电镀镍和金
与上述的类似,我们的封装仅由4种材料组成(芯片、凸点、陶瓷和NCP)。这一简单结构实现了尺寸小、薄而重量合适的封装。
可用的陶瓷基板材料主要有二种:HTCC(高温共烧陶瓷)和LTCC(低温共烧陶瓷)。陶瓷的特性(如电特性、温度传导性、CTE和翘曲性)及倒装芯片键合,使我们的封装能满足从电器产品到半导体芯片广泛要求的最佳解决方案。
MonsterPAC-typeC结构的特点
特点如下:
● 无损伤键合
● 高热辐射
● 低插入损耗
● 高可靠性
将每一个主要优势结合起来,MonsterPAC-typeC能实现20nm一代LSI的最好性能。
无损伤键合
我们的封装的核心技术是无损伤倒装芯片键合技术,此技术对尖端精细工艺制造的半导体芯片实现无损伤和高可靠性键合。
半导体芯片无损伤指的是:
低压力键合
我们的键合压力能达到0.12g/凸点,是常规C4的2.4g/凸点的1/20。通过使键合负载减少到这个极限,可防止键合引起的层间介质的损伤。
凸点固化过程中的回缩应力低
凸点固化过程中的回缩应力低于10MPA/凸点,非常小。通过最大限度减少加于易脆介质中间层(如低k和Al焊盘及线条等等)的温度、负载和回缩应力,防止线条的断裂与裂缝,从而实现高良率和可靠的倒装芯片键合。
从这些优势可见,其是唯一具有防止脆弱低k层损伤的结构的封装。
高热辐射
认识到半导体芯片的热量是通过封装基板辐射的,替代常规的有机基板(热导率0.5W/mk),我们选择陶瓷基板,因为其热导率超过有机基板,为14W/mk。当封装尺寸是21×21mm,用陶瓷基板时,功率耗散达到6W,比功率耗散为3.6W的有机基板提高1.7倍。
低插入损耗
电子设备要求在高频范围有高水平性能。陶瓷基板的插入损耗是0.42dB(@20GHz,L=5mm),而有机基板的是0.62dB,陶瓷基板允许的频率在10GHz以上,而有机基板是3GHz。
抗潮湿的高可靠性和高耐受性
一般的抗回流焊(MSL:湿度敏感等级)是Level 3(@30deg/60%RH192Hr)。MonsterPAC-typeC对半导体芯片是无损伤的,凸点用非熔材料制成。高温回流焊时,凸点是不熔化的,所以它不重复再熔化和再固化,陶瓷基板不吸收湿气。结果,MonsterPAC-typeC是MSL Level 1(@85deg/85%RH192Hr),它不需要预烘烤去湿和防潮包装,MonsterPAC-typeC的车间寿命是无限的。
工厂效率高
替代焊接凸点,我们开发了易于生产的环氧凸点结构。结果,很多晶圆凸点工艺用的设备就不必要了,消耗大量能量的焊接连接用回流焊也不必要了。所以,与同等规模的常规C4工艺工厂比较,工厂面积能减少69%,工厂的能耗减少85%。能实现节能和低环境负荷工厂。
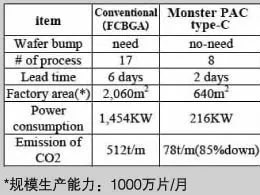
MonsterPAC-typeC工艺的特点
陶瓷技术凸点
MonsterPAC-typeC采用含银的导电浆料作为凸点材料。采用普通焊接印刷SMD零件的印刷技术在陶瓷基板上形成凸点。凸点处理前陶瓷基板表面的预处理、清洗处理和凸点形成后凸点的表面电镀都没有必要了。而常规有机FCBGA需要在半导体晶圆芯片的Al焊盘上长凸点,如焊剂、Au和Cu凸点。但基于陶瓷技术的凸点不需要这些晶圆长凸点工艺,而是在半导体芯片上制作非电镀Ni和Au。基于陶瓷技术的凸点实现了处理简易且成本低的工艺。
此外,与常规技术中使用的焊剂、Au和Cu凸点等硬凸点(硬度≥10Hv)不同,开发了在低硬度下能保持形状的软凸点(≤1Hv)。
关于含银软凸点导电浆料,我们开发的关注点是低应力、低连接电阻和细节距印刷能力。我们目前凸点形成的生产能力是面阵列焊盘:节距150μm;周边焊盘:节距75μm。但是,此焊盘节距是实际设计规则所考虑的,所以,对于仅创建凸点来说,面阵列节距60μm是可以使用的。
无损伤键合
用软倒装芯片键合技术,以前的NCP分配给用陶瓷上凸点技术形成的软凸点,然后,半导体芯片用倒装芯片键合。键合过程中,凸点的导电浆料和NCP同时固化,结果,连接性与可靠性二者均得以实现。
键合时,FCB设备的温度在200℃以下,此温度比常规键合技术低40℃以上,键合压力低于0.12g/凸点,是常规键合技术的1/20。用这些低温低压力的热压键合,半导体芯片在键合及键合后固化时没有受到应力和外力。采用新开发的导电浆料和NCP,实现了1.0 秒以下的高速键合时间。在NCP中含有填充剂,倒装芯片键合时,填充剂存在于芯片焊盘和凸点的二侧。不过,用低压力倒装芯片键合时,填充剂埋藏在凸点内,所以不影响芯片焊盘与凸点间的连接。这是软凸点的一个优点。又通过倒装芯片焊接前NCP的分配,NCP很容易填充在凸点窄隙间,用低负载键合时芯片与基板的对准就不会发生。所以,这种键合技术适用于窄焊盘节距。
常规键合技术的问题是,在焊接凸点的倒装芯片键合情况下,焊剂从熔化到固化时,很大的回缩应力(约200-500MPa/凸点)加于半导体芯片的凸点和Al焊盘上。但是,由于非熔化凸点材料及低弹性模量使得回缩应力非常小(低于10MPa/凸点),结果就实现了低应力键合技术。
由于上述工艺的这些基础技术的进展,实现了无损伤倒装芯片键合。图4是倒装芯片键合后凸点视图和连接的截面图。
可靠性
封装级可靠性
可靠性测试以下列条件评估,显示测试结果。
被测试封装规格:
芯片尺寸:5×5mm2
凸点规格:150μmP/784凸点(28×28)面阵列菊花链
基板尺寸:15×15mm2
终端规格:0.65mmP/468针脚(22×22)
样品尺寸:22pkg/批×3批
电测试方法
可靠性测试采用菊花电路测试工具。在某一段间隔和调节周期或小时数时的可靠性测试后测量电阻。增加超过5%时认为是失效,以此为准则。
是1500个TC测试后凸点的截面图,没有检测到会引起断开连接的裂缝和剥层。
板级可靠性测试
具有某些封装尺寸和焊盘节距组合的DUT安装在母板上,此板以热循环测试方法进行测试。
热循环条件是:-40℃/15分钟~125℃/15分钟循环。
不管封装尺寸和焊盘节距如何,经1000个热循环测试后,没有发现任何失效。中,首次失效的原因是BGA焊球连接。
比较了影响MonsterPAC-typeC,C4和C4柱封装可靠性的因素。
采用低弹性模量材料,MonsterPAC-typeC实现了低翘曲结构和对温度的稳定翘曲。所以,凸点与芯片Al焊盘之间连接的应力非常小,MonsterPAC-typeC是具有易脆低k层的高可靠性封装。
产品举例
采用MonsterPAC-typeC的产品例子如下:
APIC(应用处理器IC)
现今APIC的加工正向使用低k材料的精细加工转移,这需要高温度耐受性和高速度。MonsterPAC-typeC以下列优势能满足这些要求。
● 无损伤键合
● 高热辐射
● 高速度
一些APIC客户正对MonsterPAC-typeC进行评估,准备规模生产。
作为在同样条件(同样的服装,同样的芯片和同样的焊盘节距)下,有机FCBGA和MonsterPAC-typeC之间实际评估结果,MonsterPAC-typeC的温度Tj比有机封装的温度低10℃。通过精确比较Tj,其差异将为约20℃。
RF模块
当前对于高速通讯LSI,模块封装不断增长。这些模块要求下列特性:
● 适用于高速和高频
● 尺寸小
对于高速高频应用,如上所述,采用陶瓷基板后可改善插入损耗,可用于10GHz。
此外,由于可获得封装小、细节距倒装芯片键合,所以,多芯片和高数量的SMD零件可用于小封装内。
与一些RF模块客户合作,开发了一些样品,其性能已被客户认可,正准备规模生产。
对于这些模块封装,基板的湿度控制是很重要的。MonsterPAC-typeC的MSL是Level 1,所以无湿度控制。
可见,MonsterPAC-typeC是最适合用于模块封装的,对于常规有机封装的SMD和倒装芯片这种模块封装需要多次再流焊。
结论
对于即将到来的20nm工艺一代,封装要求适应更高的热辐射和更高的速度。但是,常规的封装技术难以满足这些要求。所以需要开发能适应20nm工艺一代的新封装技术。
我们开发的MonsterPAC -typeC能适应即将来到的20nm工艺一代,能使LSI性能最大化。它具有的高性能就像是一个令人惊奇的怪异产物。我们开发的MonsterPAC使C4技术成为过时的东西,成了贡献给未来下一代半导体的主要技术。
用于下一代的技术开发
新陶瓷基板的开发
陶瓷基板的技术开发很长时间进展不明朗。目前,精细而高密度作图远落后于有机基板。
为了解决作图的这一弱点以向前进步,我们开始开发精细的高密度陶瓷基板,而又不影响成本。我们的目标是20μm线条节距,达到采用精细图形的更灵活设计,通孔节距也需要更精细,目标是50μm。
目前陶瓷基板的制造工艺是采用冲孔和掩膜印刷。现有的这些工艺对于精细作图的局限性很大。我们正考虑用激光和直接印刷法工艺替代它们。成功实现这一技术将提供比有机基板好得多的性能。到目前为止,陶瓷基板一般用于高端产品,不过,这种新基板将面向消费产品。而这种基板也的确需要高性能消费产品来壮大自己。
这一基板与MonsterPAC技术的结合将为世界提供最佳性能和高可靠性的产品。